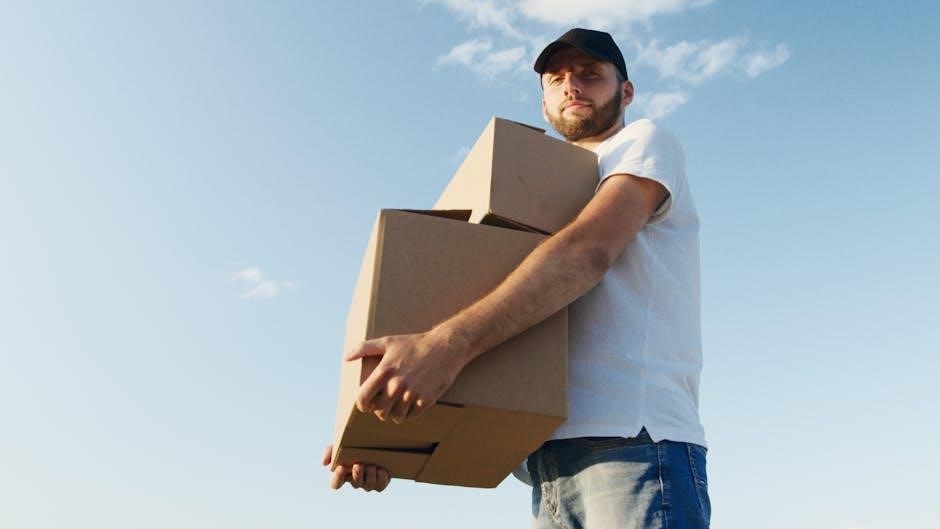
what does tile stand for manual handling
What Does TILE Stand For in Manual Handling?
In manual handling, TILE is an acronym used to aid risk assessment․ It stands for Task, Individual, Load, and Environment․ This approach enables systematic evaluation, helping employees and employers plan manual handling activities safely, minimizing workplace injuries and promoting overall well-being․
Manual handling in the workplace presents numerous risks, making it crucial to implement effective risk assessment strategies․ TILE is an acronym that serves as a valuable tool in this context․ It represents Task, Individual, Load, and Environment, and it provides a structured approach to evaluating and mitigating risks associated with manual handling activities․ Understanding the TILE process is fundamental for conducting thorough risk assessments and creating safer work environments․
By considering each element of the TILE acronym, employers and employees can systematically identify potential hazards and implement appropriate control measures․ The Task element focuses on the specific actions involved in the manual handling activity․ The Individual element considers the capabilities and limitations of the person performing the task․ The Load element assesses the characteristics of the object being moved, such as its weight, size, and stability․ Finally, the Environment element examines the surrounding conditions, including space constraints, lighting, and floor surfaces․
The TILE approach promotes a proactive safety culture, empowering workers to assess risks before engaging in manual handling tasks․ This approach helps protect employee safety by encouraging them to assess a task systematically before they begin․ Properly implemented TILE strategies contribute to reducing the incidence of musculoskeletal disorders and other injuries․
The Meaning of Each Letter in TILE
TILE is an acronym that encompasses key elements for manual handling risk assessment․ Each letter represents a critical factor: Task, Individual, Load, and Environment․ Understanding each component’s meaning is essential for effective and comprehensive risk management in the workplace․
T: Task
The ‘T’ in TILE stands for Task, representing a detailed examination of the manual handling activity itself․ This involves scrutinizing various aspects, such as the frequency of the task, the distances involved in moving objects, and the heights at which items are lifted or carried․ Repetitive movements, awkward postures required by the task, and any twisting or bending motions are all crucial considerations․
Analyzing these elements helps identify potential hazards associated with the task․ For instance, frequent lifting of heavy objects over long distances, or performing tasks that require sustained awkward postures, can significantly increase the risk of musculoskeletal injuries․ A comprehensive task assessment forms the foundation for implementing appropriate control measures․
By understanding the specific demands of the task, employers can implement strategies to minimize risks․ This might include redesigning the task to reduce physical strain, providing mechanical aids to assist with lifting and carrying, or implementing job rotation to reduce exposure to repetitive movements․ Evaluating the task is a fundamental step in ensuring a safe working environment․
I: Individual
The ‘I’ in TILE signifies the Individual, emphasizing the importance of considering the person performing the manual handling task․ This involves assessing their physical capabilities, such as strength, fitness level, and any pre-existing health conditions that could affect their ability to perform the task safely․ Factors like age, experience, and training are also relevant considerations․
A proper assessment ensures the individual is capable of handling the physical demands of the job without undue risk of injury․ Individuals with prior musculoskeletal issues may be more susceptible to injury when performing certain manual handling tasks․ Providing appropriate training on safe lifting techniques and the use of equipment is vital to protecting employees․
Adjustments may be needed to accommodate individual limitations․ This could include modifying the task, providing assistive devices, or assigning different tasks that are better suited to their capabilities․ Ignoring individual factors can lead to increased risk of strain, sprains, and other musculoskeletal disorders, highlighting the importance of a comprehensive individual assessment․
L: Load
The ‘L’ in TILE represents the Load, which refers to the object being handled․ Assessing the load is crucial in manual handling risk assessment․ This involves evaluating several characteristics, including the weight, size, and shape of the load․ A heavy or bulky load can significantly increase the risk of injury, especially if it’s difficult to grip or maneuver․
The stability and contents of the load are also important considerations․ Unstable loads can shift during handling, leading to loss of balance and potential injury․ Hazardous contents require special precautions to prevent exposure or spills․ The frequency and duration of handling the load should be assessed․
Repetitive handling of even light loads can cause strain over time․ Consider whether the load has handles or grips to facilitate safe handling․ Poorly designed packaging can make a load unnecessarily difficult to handle․ Implementing measures such as using mechanical aids, reducing the load weight, or improving packaging can minimize risks associated with the load․
E: Environment
The ‘E’ in TILE stands for Environment, encompassing the physical surroundings where manual handling takes place․ A thorough evaluation of the environment is crucial for identifying potential hazards and minimizing risks․ Factors to consider include the available space, floor conditions, lighting, and temperature․ Confined spaces can restrict movement and increase the likelihood of awkward postures, while slippery or uneven floors can lead to slips and falls․
Inadequate lighting can impair visibility, making it difficult to see hazards or handle loads safely․ Extreme temperatures can affect workers’ performance and increase the risk of heat stress or cold-related injuries․ Obstructions, such as equipment or clutter, can create tripping hazards or impede movement․ The presence of stairs, ramps, or other changes in elevation should be carefully assessed, as they can pose additional challenges․
Weather conditions, particularly in outdoor environments, can significantly impact manual handling tasks․ Rain, snow, or ice can make surfaces slippery and increase the risk of accidents․ Proper planning and implementation of control measures, such as providing adequate lighting, maintaining clear pathways, and using appropriate personal protective equipment, can help create a safer working environment;
How TILE Aids in Risk Assessment
TILE aids risk assessment by providing a structured approach․ It prompts consideration of Task, Individual, Load, and Environment․ This systematic evaluation helps identify potential hazards, allowing for proactive measures to protect employee safety before manual handling tasks commence․
Systematic Evaluation
TILE’s strength lies in its systematic approach to evaluating manual handling risks․ By breaking down the assessment into four key components – Task, Individual, Load, and Environment – it ensures a comprehensive review of all potential hazards․ This structured methodology prevents overlooking critical factors that could contribute to injuries․
The “Task” element prompts an examination of the specific actions required, identifying repetitive movements, awkward postures, and excessive reaches․ Assessing the “Individual” involves considering the worker’s capabilities, experience, and any pre-existing health conditions․ Evaluating the “Load” focuses on its weight, size, shape, and stability․ Finally, analyzing the “Environment” takes into account space constraints, floor conditions, lighting, and temperature․
This systematic evaluation allows for a more thorough understanding of the risks involved, enabling the implementation of targeted control measures․ By addressing each component of TILE, employers can develop safer work practices, provide appropriate training, and modify the work environment to minimize the likelihood of manual handling injuries․ Ultimately, TILE’s systematic approach fosters a proactive safety culture․
Protecting Employee Safety
The TILE framework plays a crucial role in protecting employee safety during manual handling tasks․ By implementing TILE, employers can proactively identify and mitigate potential risks before injuries occur․ This approach fosters a safer work environment, reducing the likelihood of strains, sprains, and other musculoskeletal disorders commonly associated with manual handling․
By systematically evaluating the Task, Individual, Load, and Environment, TILE enables employers to tailor risk control measures to specific situations․ This targeted approach ensures that interventions are effective and address the unique challenges of each manual handling activity․ For example, if the “Load” is excessively heavy, measures such as providing mechanical aids or reducing the load weight can be implemented․
Furthermore, TILE promotes employee involvement in the risk assessment process․ By encouraging workers to consider the Task, Individual, Load, and Environment, they become more aware of potential hazards and are empowered to suggest improvements․ This collaborative approach fosters a safety culture where employees actively participate in protecting their own well-being and that of their colleagues․ Ultimately, TILE contributes to a healthier, safer, and more productive workforce․
Variations of TILE: LITE
While TILE (Task, Individual, Load, Environment) is a widely recognized acronym for manual handling risk assessments, variations exist to suit different organizational needs or to emphasize specific aspects of the process․ One such variation is LITE․ LITE serves as a mnemonic to guide the risk assessment process, prompting users to consider key factors․
The acronym LITE rearranges the elements of TILE, focusing on Load, Individual, Task, and Environment․ The subtle shift in emphasis highlights the significance of the load being handled and its impact on the individual performing the task․ This variation may be particularly useful in environments where the characteristics of the load pose a substantial risk, such as in warehouses or construction sites․
The choice between TILE and LITE often depends on the specific context and the preferences of the organization conducting the risk assessment․ Both acronyms provide a structured framework for identifying and mitigating hazards associated with manual handling, ultimately contributing to a safer and healthier workplace․ It’s important to understand both to choose the most appropriate tool․
Implementing TILE in the Workplace
Successfully implementing TILE (Task, Individual, Load, Environment) in the workplace requires a comprehensive and proactive approach․ It begins with educating employees about the meaning of TILE and its role in preventing manual handling injuries․ Training sessions should cover each element of TILE, providing practical examples and demonstrating how to apply the framework to real-world scenarios․
Next, integrate TILE into existing risk assessment procedures․ This involves incorporating TILE considerations into job safety analyses and pre-task planning․ Encourage employees to use TILE as a checklist to identify potential hazards before undertaking any manual handling activity․
Furthermore, foster a culture of open communication where employees feel comfortable raising concerns about manual handling risks․ Regularly review and update TILE-based risk assessments to reflect changes in work processes, equipment, or the work environment․
Finally, leadership commitment is crucial․ Managers and supervisors should champion the use of TILE and provide the necessary resources to support its implementation․ By consistently applying TILE, organizations can create a safer and more productive workplace for all employees․